There is a high attention in the life science industry on qualification of equipment and validation of processes based on comprehensive risk management processes and the employees are usually well-trained in these tools. Errors and deviations are handled by using systematic problem-solving methods to reveal the true root cause(s) and identify the appropriate corrective actions.
The team members involved in the problem-solving process have normally good knowledge of the machines, tools, materials, methods and procedures.
When it comes to Manpower the knowledge is more limited.
The traditional way of looking at causes related to Manpower is that these errors are caused by unreliable people in well- designed systems.
To protect the system from the unreliable “human behavior” typical corrective actions are:
- Tighten procedures to reduce the bandwidth in which people operate
- Introduce more technology to monitor or replace human work
- Make sure that the “unreliable” person(s) do not contribute to system breakdown again by training, reallocation of position etc
Tighten procedures might reduce the risk for human errors but not necessarily. It can increase the mismatch between procedure and practice. More technology might remove risk for certain human errors but can introduce risks for other types of human errors.
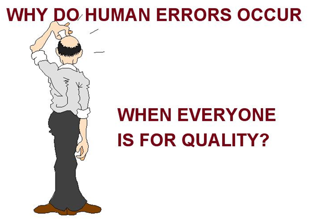
People are not unreliable, but we all have some human limitations which have impact on our decisions, actions and performance.
Examples of human limitations
- Attention – may be limited in duration or focus, especially if attention must be spread
- Memory – working memory is limited, especially when active processing of information is required
- Situation awareness – refers to a person’s perception of what’s happening around them
- Automaticity – consistent, over-learned responses may become automatic and completed without conscious thought
- Stress – occurs when there is a mismatch between what people are expected to do or cope with and the resources available to them
- Tiredness – caused by too much or too little to do, sustained activity, physical / emotional exertion, amount / quality of sleep, time of day
- Cognitive BIAS
When investigating human errors, it is important to evaluate if your system and/or processes are designed to fit human capabilities and limitations in perception and cognition.
To be able to do this, it requires that the persons involved in systematic problem-solving have some basic training in human behavior based on behavioral economics. I have not seen this yet as a requirement in any competency matrix.
I hope that we in future will have much more focus on designing working environment, processes and quality management systems which supports the human nature with all our cognitive limitations and bias’.
I am convinced that it will pay-off by higher quality performance and more satisfied employees.